To understand the chances that the US will succeed, MIT Technology Review spoke to Shawn Qu. As the founder and chairman of Canadian Solar, one of the largest and longest-standing solar manufacturing companies in the world, Qu has observed cycle after cycle of changing demand for solar panels over the last 28 years.
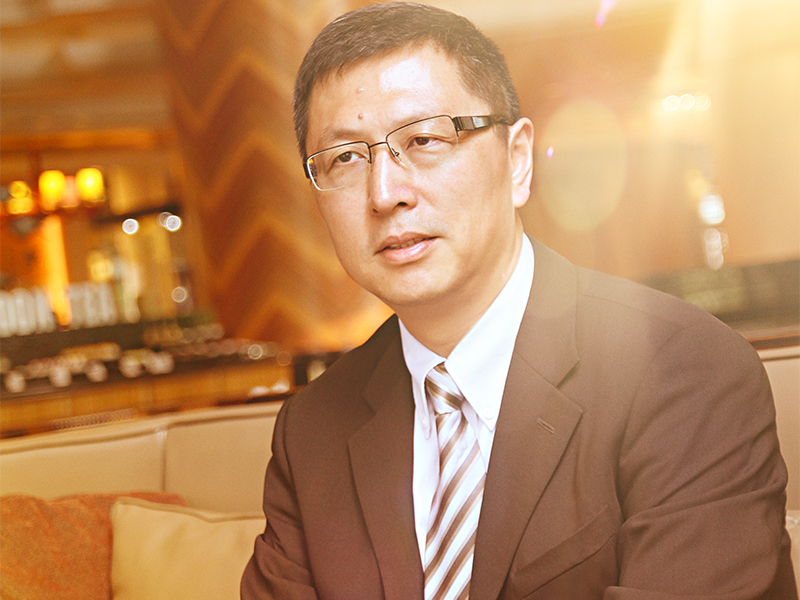
CANADIAN SOLAR
After decades of mostly manufacturing in Asia, Canadian Solar is pivoting back to the US because it sees a real chance for a solar industry revival, mostly thanks to the Inflation Reduction Act (IRA) passed in 2022. The incentives provided in the bill are just enough to offset the higher manufacturing costs in the US, Qu says. He believes that US solar manufacturing capacity could grow significantly in two to three years, if the industrial policy turns out to be stable enough to keep bringing companies in.
How tariffs forced manufacturing capacity to move out of China
There are a few important steps to making a solar panel. First silicon is purified; then the resulting polysilicon is shaped and sliced into wafers. Wafers are treated with techniques like etching and coating to become solar cells, and eventually those cells are connected and assembled into solar modules.
For the past decade, China has dominated almost all of these steps, for a few reasons: low labor costs, ample supply of proficient workers, and easy access to the necessary raw materials. All these factors make made-in-China solar modules extremely price-competitive. By the end of 2024, a US-made solar panel will still cost almost three times as much as one produced in China, according to researchers at BloombergNEF.
The question for the US, then, is how to compete. One tool the government has used since 2012 is tariffs. If a solar module containing cells made in China is imported to the US, it’s subject to as much as a 250% tariff. To avoid those tariffs, many companies, including Canadian Solar, have moved solar cell manufacturing and the downstream supply chain to Southeast Asia. Labor costs and the availability of labor forces are “the number one reason” for that move, Qu says.
When Canadian Solar was founded in 2001, it made all its solar products in China. By early 2023, the company had factories in four countries: China, Thailand, Vietnam, and Canada. (Qu says it used to manufacture in Brazil and Taiwan too, but later scaled back production in response to contracting local demand.)
But that equilibrium is changing again as further tariffs imposed by the US government aim to force supply chains to move out of China. Starting in June 2024, companies importing silicon wafers from China to make cells outside the country will also be subject to tariffs. The most likely solution for solar companies would be to “set up wafer capacity or set up partnerships with wafer makers in Southeast Asia,” says Jenny Chase, the lead solar analyst at BloombergNEF.
Qu says he’s confident the company will meet the new requirements for tariff exemption after June. “They gave the industry about two years to adapt, so I believe most of the companies, at least the tier-one companies, will be able to adapt,” he says.