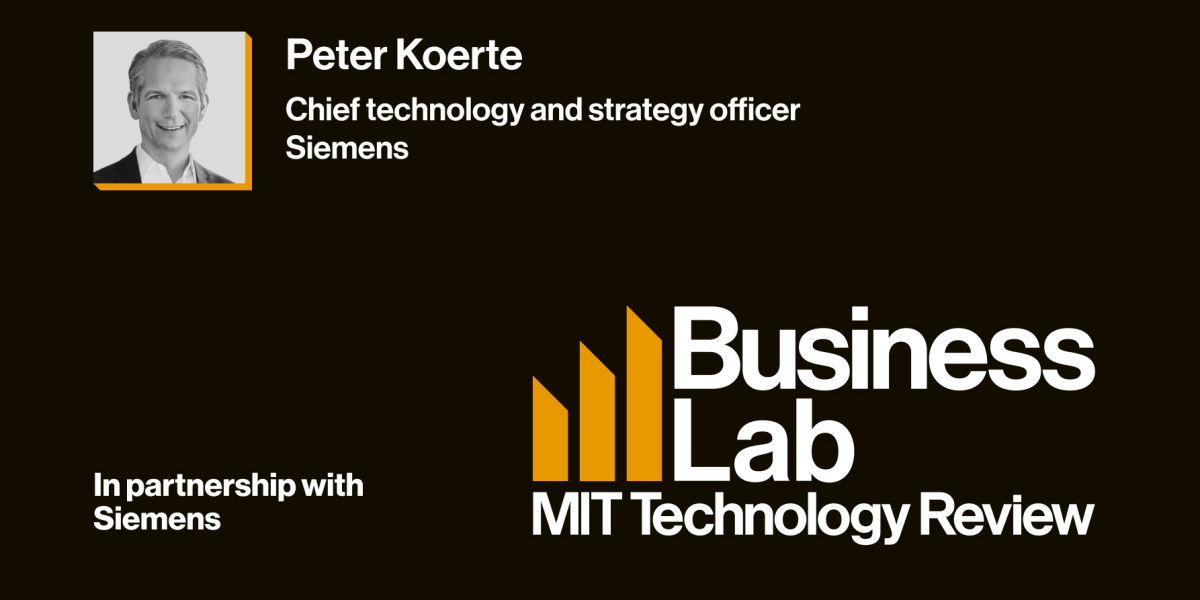
Peter: Yeah, I know. That is indeed a big question and we get that question a lot nowadays, particularly because of crypto and cryptocurrency and the whole notion of proof of work and the way it works. It’s very, very energy consuming, that’s true, but I think we are all in agreement that maybe that’s not the best value or time spent on making this work. In the case of the industrial metaverse, we believe that it is actually substantially helpful to have those simulations in the digital world first and then put them into the real world.
From the numbers I know, ICT (information and communication technologies) contributes about 4% to greenhouse gas emissions. Now, there’s other studies that I’m aware of that would suggest that up to 40% of greenhouse gas emissions can be reduced because of the digitalization effect, which we do think is possible. So there you go. It’s a factor of one to 10 in terms of leverage. So, yes, there is some element where you have to invest into it and probably create a little bit more greenhouse gases, but the net effect is absolutely very much in favor of doing it.
Last point on this one, the key thing today is that we need to understand the carbon footprint that we are leaving behind. Today that is a gross estimation. Today we say, “Well, around about 50 gigatons of CO2 equivalents are being emitted every year.” But that’s a simulation, that’s an estimation. We really don’t know. That’s not the real number, but you need to get to the real number. So what we’ve done is we created a low-energy blockchain, which uses as much energy as two clicks on a webpage. That enables you to communicate your product’s carbon footprint between different manufacturers, so that at the very end of the chain, you can actually sum up all the carbon footprint, based on true values, so that you know, for example, how much of a carbon footprint your smartphone produces. That is the step we need to take first, so the baselining of the carbon in the designs, before we are actually going then to the reduction.
Laurel: There’s also something to be said, too, that by having the digital twins and this industrial metaverse opportunity, then things like trains and cars and other large manufacturing facilities could be then made more sustainable themselves, because you are able to do it in this environment of simulation. Does that sound right?
Peter: Yeah, absolutely, absolutely. We tend to think about, if you like, the green digital twin. Think about a designer today. What does a designer do? The designer usually has a time schedule. You have to design this product by X. It must not cost more than Y, and it has to serve these functional properties, in terms of it has to go that fast or it has to be that stiff by Z. That’s the way it goes. We think there’s now a fourth dimension and that is the green aspect, so the green digital twin where you say, “And it must not exceed that many tons or kilograms of CO2.” This is where you have now an additional element of optimization that has to come into it. It’s a trade-off, isn’t it? That’s what is happening as we speak, and those calculation tools enable you to come to the best trade-off, as I said, before you even build these devices, buildings, factories, what have you.
Laurel: We’ve gone over some of the benefits of digitalization of industrial IoT (Internet of Things) in the industrial metaverse: data, time to market, responsiveness to customers, as well as this ability to improve sustainability, but what are some of the challenges? Why aren’t we all there yet?
Peter: Well, as always, there are many. First and foremost, there are of course the legacy systems. Every company has its own IT systems, its own configurations, so, therefore, most of the technology that we want to implement of course is not scaling the way it should and could. Second, very often there’s no interface, either from the machine where you can extract the data or from the software where the data resides. This whole notion of being open and being able to access other applications’ data is really a key obstacle. To me, to sum this all up, it’s really the whole question about interoperability.
We just recently launched what we call the Siemens Xcelerator, which is a digital business platform where we promote portfolio elements. So solutions that are truly open, where you have interfaces, so-called application programming interfaces (APIs), that are open. They’ll describe where others actually can build atop of it, and that are also very flexible so that you can install them in existing brownfield environments. That is really the biggest challenge in the industrial world.